SLS has been widely used in soap and shampoo, but now it was mostly replaced by its
ethoxylated derivative - Sodium Lauryl Ether Sulfate (SLES). Despite concerns over the safety of SLES coming from scientists and research groups; these chemicals continue to be the darlings of manufacturers of household products because they’re cheap and they perform a simple task really well. They make long-lasting bubbles and it’s hard for us to get away from the idea that more bubbles equals better cleaning power. As a result SLES is used in hundreds of products, from dishwashing liquid to shampoo. Even some ‘eco’ brands use these chemicals.
Machinery
and Technology
Sulphonation processing and advantages
1. Molten sulphur system
The sulfur melting unit is equipped with a molten sulfur trough and a liquid sulfur trough. Fusedsulfur tanks are installed below the ground level, and the upper part of the tank is flush with the ground level, which facilitates manual dumping of solid sulfur. The liquid sulfur high position tank is installed above the ground level to facilitate the maintenance of the sulfur insulation jacket pump and filter. The solid sulfur is melted in the molten sulfur tank and lifted to the liquid sulfur high tank by a submerged pump.
2. Air Drying System
In the sulphonation system process, the air is generated by a Roots blower; the fan uses an inverter to control the system pressure automatically. The process air is pressurized by a Roots blower and then cooled by a water cooler (circulating water cooling system), followed by a glycol refrigeration liquid cooling system and then into a silica gel drying system. The dew point of the dried process air reaches below -80°C. The circulating water cooler and glycol cooler are set together with the glycol tank. Silica gel dryer uses two split-type switches, switching pneumatic valve automatic control. Silicone is regenerated by hot air or steam heating.
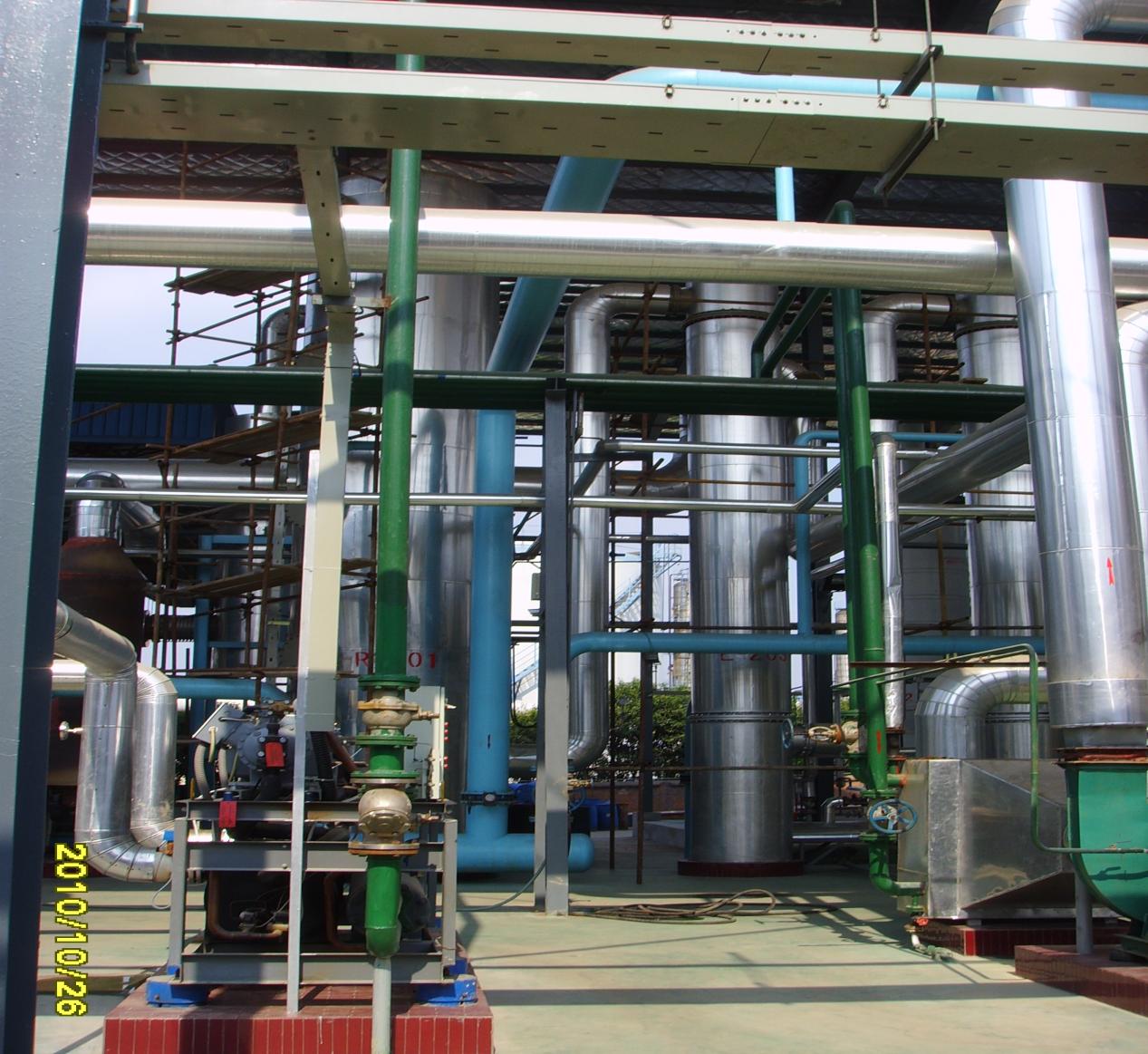
3. SO2 gas system
The liquid sulfur is quantitatively transferred to sulfur furnace controlled by the jacket
insulation metering pump or the jacket insulation gear pump along with the mass flow meter. After burning, the SO2 gas with a temperature of 650℃ passes SO2 cooler to cool the temperature to 420℃, then this cooled SO2 gas enters into SO2/SO3 conversion tower.
4. Conversion Tower System
Conversion tower has a set of independent preheating systems, which are preheated by the oil furnace. The catalyst of each layer is heated in the conversion tower to desired temperature.
5. SO3 Cooling System
Tube-based heat exchanger is used for SO3 cooling system. The cooling air is offered by a separate fan. The waste acid discharged from the bottom of the heat exchanger is collected by a special tank, while air-pressurized instrument is used for the discharge treatment instead of oleum pump.
6. Sulphonation Reaction System
Multi-tube film Sulfonation reactor designed by our own company is used. The organic feed of each tube is controlled by high-precision rotameter, with 1.5% control accuracy regardless of the changes of tube numbers. The high-precision rotameter is easy to adjust. With the increase of number of the tubes, this advantage is more obvious. Meanwhile, in the process of production, the organic flow can be observed anytime, which indirectly helps understand whether there is any coking phenomenon in any of the reaction tube.
7. Exhaust Treatment
The exhaust from the top of the gas-liquid separator is first pre-proceeded by AEO2 absorption device. AEO2 intermediate tank is built in below the AEO2 absorption tower where a certain liquid level of AEO2 is kept. The SO3 remained in the exhaust is absorbed by AEO2, which a circulation pump is used to spray circularly. Meanwhile, the absorbed AEO2 is also provided as raw material to the sulfonation reaction device (This part is specially for producing SLES).
8. Continuous Flashing Evaporation and Neutralization Process
Pump-typed continuous neutralization is required to produce SLES with a concentration of greater than 70%. An accurate amount of ether sulfate ester is adjusted by a mass flow meter, and then enters into the continuous neutralization reaction pump inlet.
9. Waste Heat Recovery System
In the SO3 gas preparation unit, sulfur combustion in the sulfur-burning furnace will produce a high temperature of 700 ° C, and the inlet temperature of the conversion tower cannot be higher than 450 ° C, so that we will use the SO2 heat exchanger to use the temperature of the sulfurfired furnace outlet with a cooling fan.
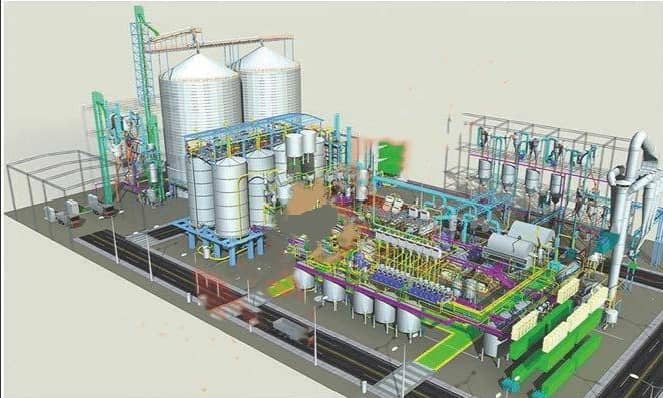